Automation and Robatic
Automate your processes to gain greater efficiencies
Maximize your production capacity with automation
Up your production game with automation
With a constant need to produce more and to do it faster while also facing the reality of a shrinking labor force, you need to leverage tools that will help you compete. Whether it’s freeing up your employees from spending time on repetitive tasks so they can focus on jobs that require more skill, improving employee safety or creating the ability to keep production going 24/7, finding the right robotic welding or cutting automation solution can help you meet your goals. And with so much to consider, you’ll want the expertise of a supplier who can guide you along your journey to produce more parts — better, faster and safer.
Industrial automation and robotics are the use of computers, control systems and information technology to handle industrial processes and machinery, replacing manual labour and improving efficiency, speed, quality and performance.
Automated industrial applications range from manufacturing process assembly lines to surgery and space research. Early automated systems focused on increasing productivity (as these systems do not need to rest like human employees), but this focus is now shifting to improved quality and flexibility in manufacturing and more. Modern automated systems are developing beyond mechanisation with the addition of artificial and machine learning.
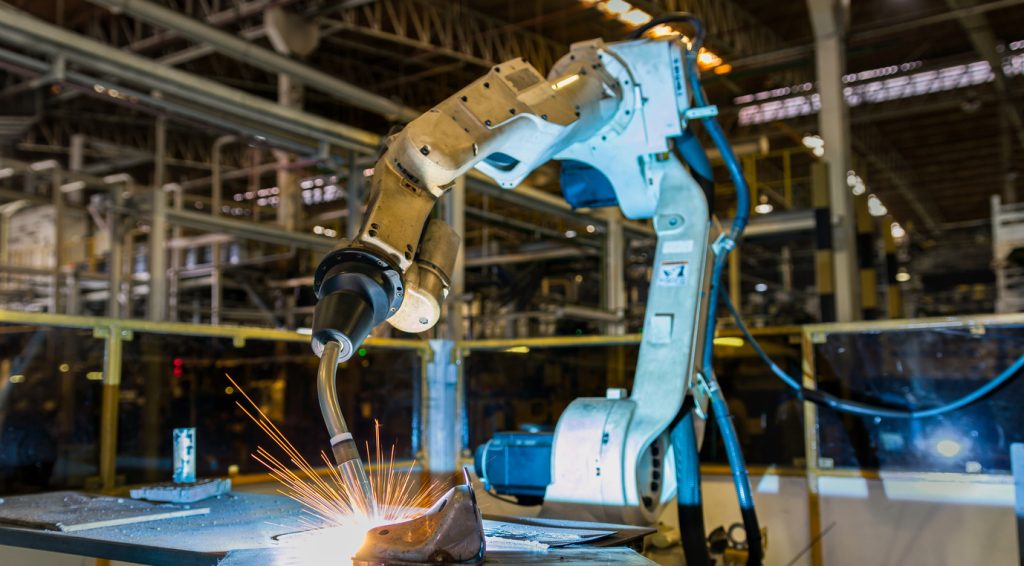
However, automation and robotics are not the same thing:
Automation
Automation is the use of computer software, machines or other technology to carry out tasks that would otherwise be done by a human. There are several types of automation, which can include both virtual and physical tasks.
Robotics
This area of engineering uses multiple disciplines to design, build, program and use robots. Robots are programmable machines that use sensors and actuators to interact with the physical world and perform actions autonomously or semi-autonomously. Because they can be reprogrammed, robots are more flexible than single-function machines. Collaborative robots are designed to complete tasks in a similar manner to humans, while traditional industrial robots tend to complete tasks more efficiently than humans.
Automation and robotics have areas where they cross, such as the use of robots to automate physical tasks, as with car assembly lines. However, not all automation uses physical robots and not all areas of robotics are associated with automation.
An early form of industrial automation was the use of CNC (Computer Numerical Control) machines for high-precision aerospace manufacturing in the United States during the Second World War. Using the first industrial computing systems, the first CNC machines still required a high level of human input until they became more automated during the 1950s.
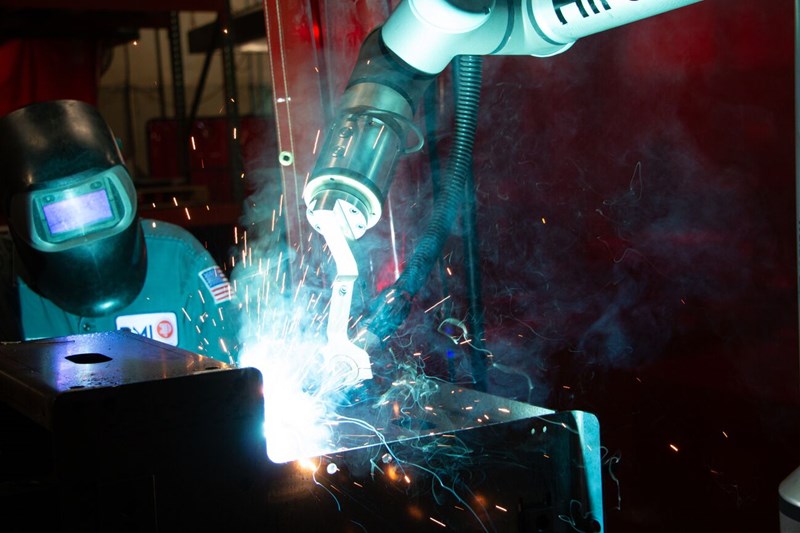
Modern industrial automation includes the use of data acquisition systems, distributed control systems, supervisory control and programmable logistics controllers. They are consistent and predictable, making them ideal for processing chemicals, pulp, paper, oil and gas or other raw materials. By adding Industry 4.0 capabilities to these systems, industrial automation can also include access to peripheral data to further optimise operations based on real-time data.
Robotic welding is a process that helps the industrial sector to automate its processes, increase accuracy, enhance safety and reduce lead time. The robot welding process is considered to be the most productive when it is implemented for high-volume and repetitive tasks. There are multiple types of robotic welding processes.
When a welding process is automated using robots, we call it robotic welding. These building robots perform and manage welding tasks based on the program and are capable of being reprogrammed as per the intended project. However, this does not eliminate human intervention as welders still control and supervise the welding robots.
Welding robots bring many benefits to the manufacturing process, including precise results, less wastage, and improved safety. These robots can reach locations that are inaccessible by human hands and perform complicated tasks much more precisely. Therefore, the time taken in the manufacturing process is minimised and greater flexibility is achieved.
There are different types of robotic welding available on the market, and the main focus should be on choosing the correct welding program for a long-lasting and durable impact.
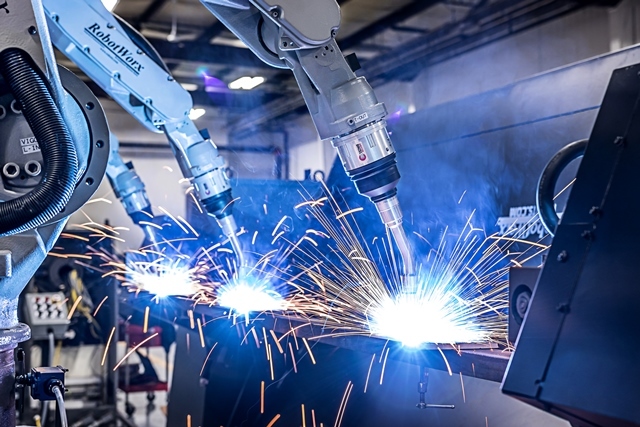
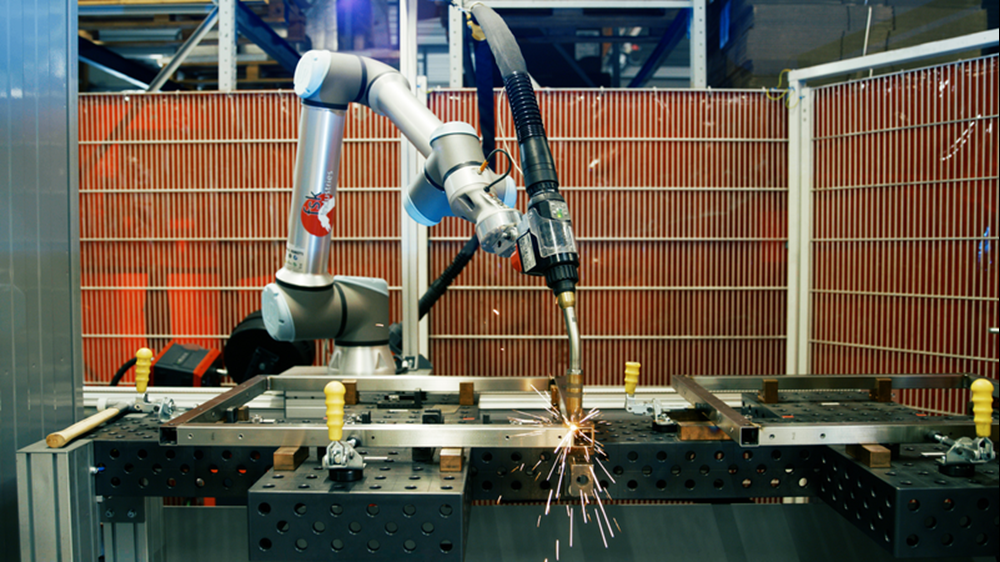