
Plasma Cutting
Plasma Cutting from 0.3 to 160 mm
Being the oldest manufacturer of plasma cutting technique in the market, Kjellberg Finsterwalde offers its customers plasma cutting technique for the most diverse tasks for automated, mechanised or manual cutting – made in Germany.
Automated Plasma Cutting
Plasma power sources used on 2D or 3D guiding systems, i.e. cutting tables, pipe cutting machines or robots, allow precise, laser-like and fast plasma cutting. Typcial application areas are the metalworking industry and steel service centres, plant and container construction or the automotive industry.
Automated plasma cutting products
K 200
With the K 200 plasma cutting system, the user focus on the essentials of plasma cutting: optimal and reliable cutting quality with easy operation at lowest costs
The plasma power source cuts with oxygen, air and nitrogen in the material thickness range from 1 up to 60 mm with a maximum cutting current of 200 A. In addition, the K 200 has a marking function. It has an integrated automatic gas control and a torch with direct connection. A hand torch extends the application range to manual cutting and gouging. Overall, the user benefits from low investment costs and easy installation, operation and maintenance of the system.
The K 200 can be fully integrated into CNC guiding systems or controlled and monitored via smartphone. The accompanying app also allows the user to see all parameters and settings at a glance and to customise cutting data.
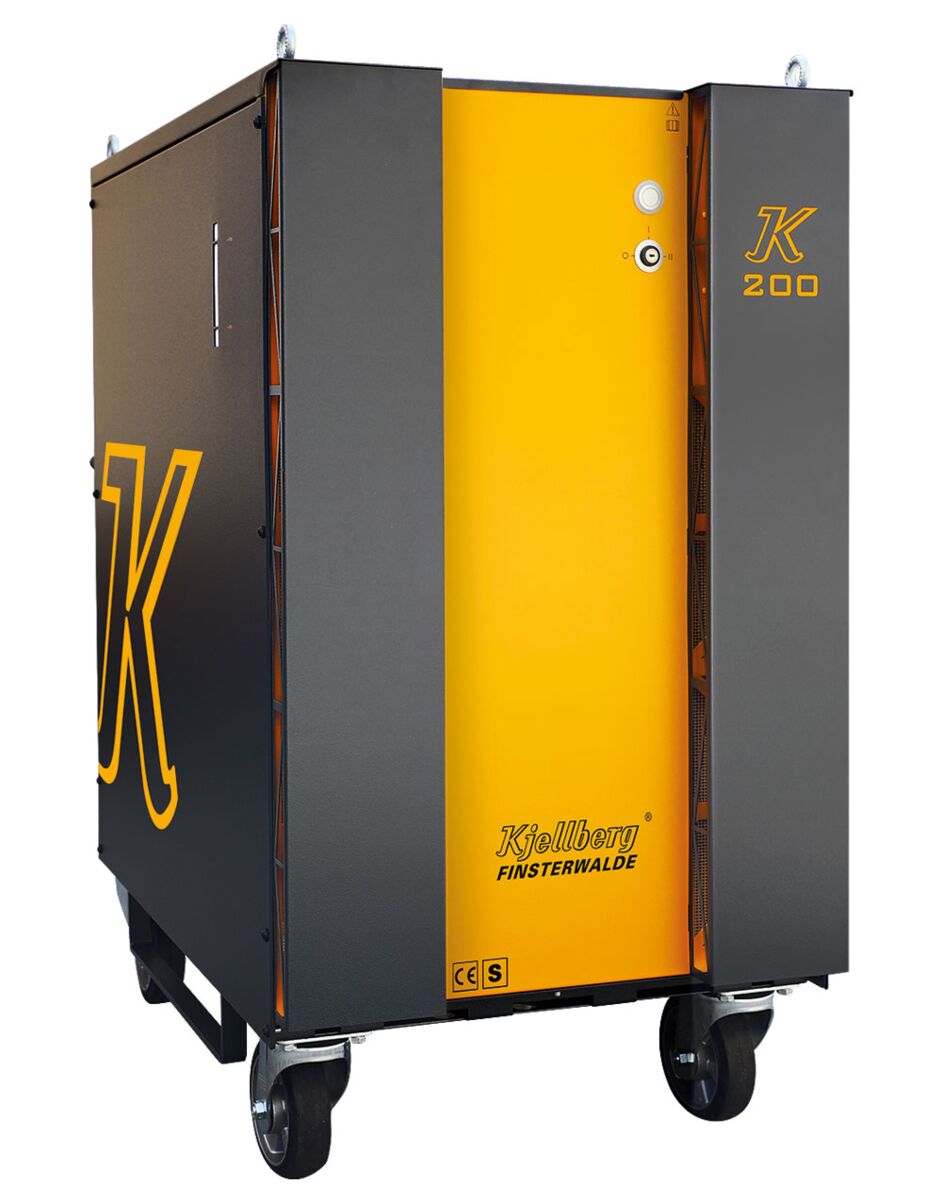
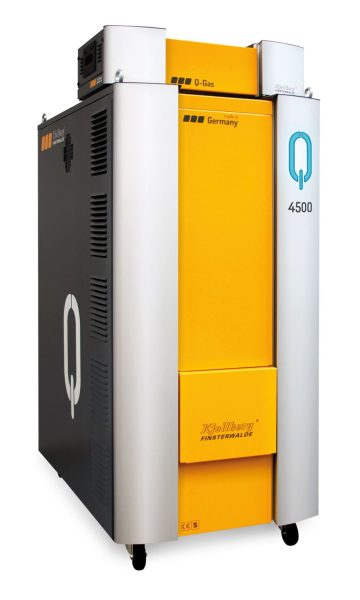
Q 4500
The Q 4500 plasma cutting system is the most powerful system in the Q-Series. It combines precise plasma cutting and marking at the best level with a maximum of 450 A cutting current. It enables the costumer to make precise plasma cuts up to 120 mm. High cutting speeds reduce costs and increase efficiency. This generation of plasma cutting systems is the result of intensive Kjellberg research and development in Kjellberg’s 100-year history. The new, digitised Q plasma system series sets forward-looking standards in quality and connectivity.
The specially developed browser-based operator interface Q-Desk provides real-time process data and information of all plant components on any standard device and location-independent. The user benefits from extensive information enabling him to plan and execute a variety of maintenance tasks as guided by the system.
The Helpcentre Q is now available for the Q-Series. Here you will find all information and documents on all power sources of the Q-Series in the currently valid version.
Smart Focus 400
With just a few settings the new plasma cutting units of the Smart Focus series achieve excellent results in the cutting range from 1 to 100 mm. Even under challenging conditions highest cutting quality and speed are realised. In such cases we use our well-proven cutting technologies, e.g. Contour Cut for cutting mild steel. The optimised gas control units and torches protect the consumables, reduce the gas consumption and, thus, the costs per cutting metre. As a further development of the Contour Cut technology the new Silent Cut technology reduces the sound pressure level by up to 15 dB(A) during cutting with currents between 60 and 160 A.
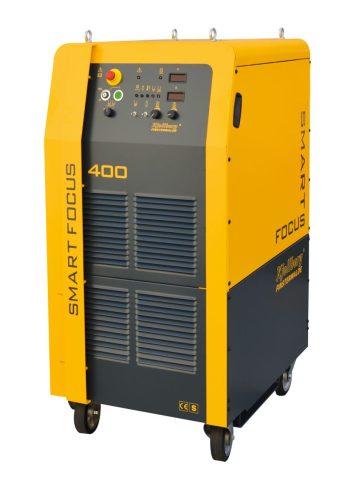
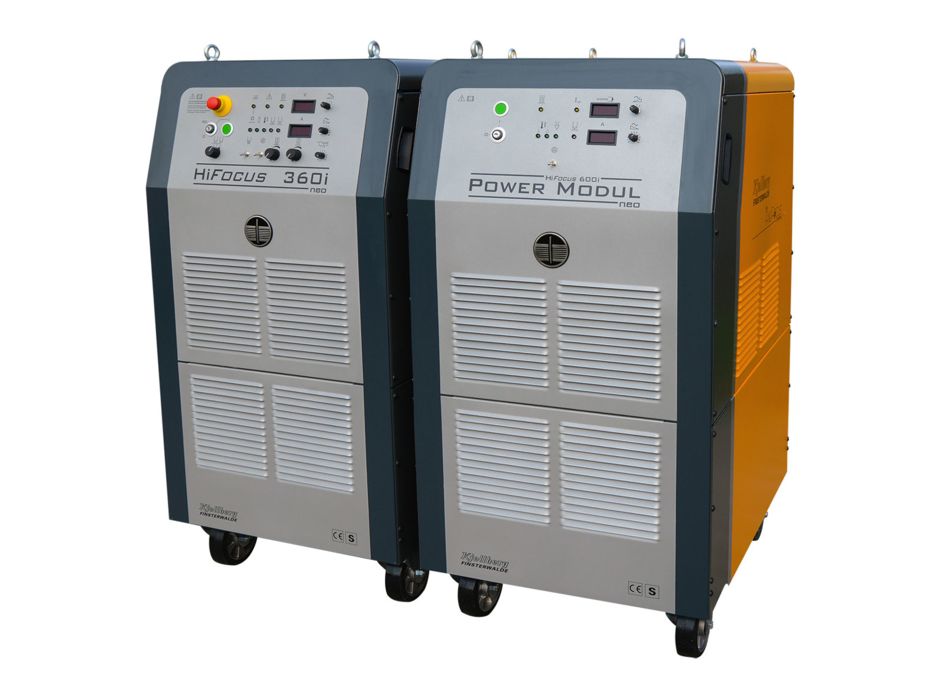
HiFocus 600i neo
The plasma cutting system HiFocus 600i neo sets new standards for plasma cutting: materials with a thickness from 0.5 to 160 mm can be cut precisely. Furthermore the system is suited for marking, bevel and underwater cutting. Consisting of two power sources (HiFocus 360i neo, power module HiFocus 600i neo) the system achieves a maximum cutting current of 600 A and can be adapted to guiding systems. With HiFocus neo the user benefits, compared to competitors, from higher speed when cutting and marking electrically conductive materials, ensuring at the same time excellent quality and low process costs. Thanks to the optimised technology, the consumables are handled gently and the plasma cutting process is more efficient. The plasma cutting system HiFocus 600i neo uses the approved Contour Cut technology for cutting contours, holes and webs fast and precisely in mild steel and can be combined with 2D as well as 3D CNC-controlled guiding systems.
FineMarker
Markings on workpieces with a plasma torch are relevant for many different applications. Later scribing on the workpiece, often done manually, can be shifted to an earlier stage of the production process as CNC-controlled scribing and marking. Due to automated marking, notching and punching of unalloyed steel, stainless steel and primed sheets, also on oily and moist surfaces, it is possible to strongly reduce valuable but ineffective downtimes in the production process. By means of plasma marking, temper colours are applied to the workpiece which are not visible anymore after colouring. By changing the parameters, the machine shifts to notching of the workpiece which is visible after colouring. Punch marks simplify subsequent boring processes or can also be auxiliary points for subsequent welding processes. The FineMarker can be adapted to CNC-controlled guiding machines and complements oxy-fuel systems as well as (older) plasma cutting machines which are not equipped for marking.
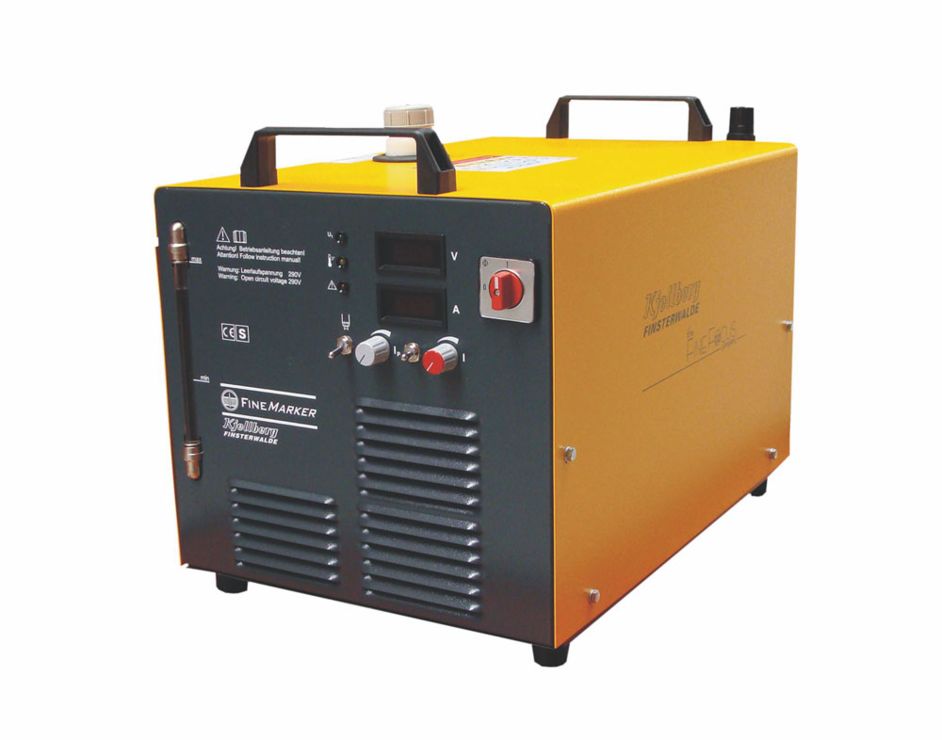