MicroStep – Your Partner for Cutting and Automation
MicroStep is one of the world’s leading manufacturers of CNC-controlled cutting systems. The group of companies develops and produces plasma, oxyfuel, laser and water jet cutting systems for its customers. from small CNC systems for schools and workshops to tailor-made production lines for steel centers, shipyards or the automotive and aviation industries. MicroStep also offers tried and tested automation solutions: from material handling around the cutting system to picking and sorting cut parts.
Expert know-how technologies
Modern cutting solutions require flexibility, precision and efficiency. For optimum results, cutting system, control system and software have to interact perfectly. More than 100 employees work at MicroStep in the in-house research department on the development and construction of CNC cutting systems and software programs. Thus, the components are optimally coordinated for a smooth operation of the systems. Whether 2D or 3D cutting (laser, plasma, oxyfuel, waterjet) or the combination of processing options (drilling, tapping, countersinking, marking, punching) on pipes, profiles, domes and flat sheets. Since control system and software solutions come from MicroStep, the software with its versatile modules can optionally be adapted to the customer’s individual requirements.
Laser cutting
The idea of the laser already goes back to Albert Einstein. But it took until the 1960s for the idea to become reality. Since then, the laser has become indispensable in many technological and scientific fields. The abbreviation laser stands for: Light Amplification by Stimulated Emission of Radiation.

Plasma cutting
With plasma technology, all conductive materials such as mild steel, stainless steel and aluminium in the medium material thickness range can be processed. Advantages of modern plasma systems are high quality cutting results, high cutting speeds, only a small heat-affected zone and the unbeatable cost-benefit ratio compared to other cutting processes.

Oxyfuel cutting
Invented as early as 1901, the oxyfuel cutting process – also known as oxyfuel flame cutting – is one of the oldest, yet most important cutting processes in the metalworking industry. In this principle of thermal cutting of steel, the metal, previously heated to ignition temperature, is oxidized with a jet of oxygen and blown out of the kerf.

Waterjet cutting
Since the beginning of the 20th century, technology has been using the power of water, first for digging gravel and clay, and in the 1930s for mining ore and coal using a high-pressure waterjet. The first waterjet cutting system followed in 1971, and today’s waterjet systems are used in a wide variety of applications. Whenever precision is required and no thermal effects are desired.
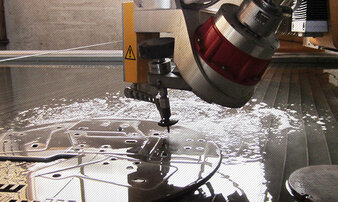